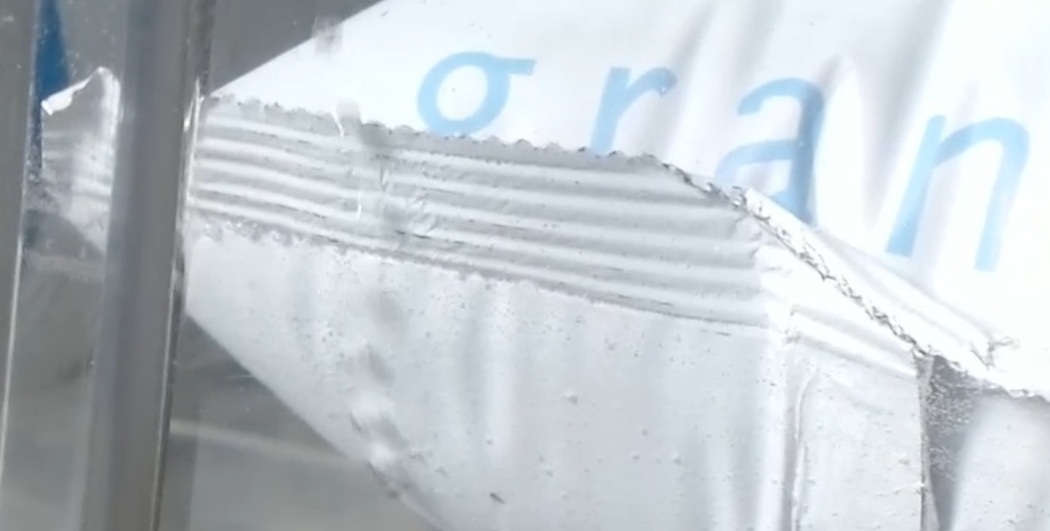
Tout d’abord, nous devons savoir ce que nous cherchons. En effet, la plupart du temps, nous cherchons à déterminer une étanchéité, mais l’étanchéité peut être définie de façon multiple : étanchéité à l’eau, étanchéité à la vapeur, étanchéité à l’air, étanchéité aux bactéries ?
Pour déterminer cette étanchéité, ce “critère”, il faut raisonner par rapport au produit qui est protégé.
Est-ce que ce produit est sensible aux bactéries ? Dans ce cas, nous allons chercher une étanchéité dont le débit de fuite se situe aux alentours de 10-4 mbar.L/s
Est-ce que ce produit est sensible à la vapeur ? Dans ce cas, nous chercherons un débit de fuite aux alentours de 10-3 mbar.L/s
Plus nous voulons aller loin dans l’étanchéité et plus la méthode de détection va être onéreuse…
Voici un petit tableau qui va vous donner quelques repères.
Critères | Taux de fuite en mbar.L/s | Diamètre de fuite |
Etanchéité à l‘eau (gouttes…) | <1,0·10-2 | Ø ≈ 100 μm |
Etanchéité à la vapeur (humidité…) | <1,0·10-3 | Ø ≈ 10 μm |
Etanchéité aux bactéries (coques, bâtonnets…) | <1,0·10-4 | Ø ≈ 1 μm |
Etanchéité à l’huile | <1,0·10-5 | |
Etanchéité aux virus | <1,0·10-6 <1,0·10-8 <1,0·10-10 | Ø ≈ 0.3 μm Ø ≈ 0,03 μm Ø ≈ 1,0 nm |
Etanchéité aux gaz | <1,0·10-8 | Ø ≈ 0.05 μm |
Etanchéité absolue | <1,0·10-12 |
Une fois que ce “critère d’étanchéité” est déterminé, on connaît la valeur approximative de la taille du trou que l’on veut déterminer. Mais cela peut être autre chose qu’un trou, on peut aussi avoir un canal, que nous appellerons capillaire qui va laisser fuir un certain débit de fuite.
C’est essentiel de mettre en rapport la taille de la fuite et le débit de fuite associé. En effet pour certaines méthodes, on va comparer le débit réel constaté sur notre échantillon avec le débit théorique à partir duquel on veut déterminer la fuite.
Une fois que ces 2 paramètres sont connus, taille de fuite et débit de fuite. Il faut mettre en concertation les équipes responsables du packaging et les équipes responsables du produit. En effet, il faut que tous les acteurs se mettent autour de la table, car il sera difficile de déterminer une étanchéité si l’on ne connaît pas le matériau utilisé pour emballer. Par exemple, tous les packagings poreux sont difficiles à évaluer par rapport à leur étanchéité, car en fonction du matériau, cette porosité est plus ou moins importante.
Il faut aussi impliquer les équipes R&D pour ne pas concevoir de packaging trop complexe à tester. Par exemple des produits qui sont très fin peuvent difficilement être percé avec une aiguille, des matériaux opaques peuvent bloquer une détection visuelle de fuite ou de pénétration de colorant.
Toutes les variables de notre équation sont importantes.
Nous connaissons maintenant parfaitement notre matériau, notre produit, la façon dont il est emballé, s’il y a de l’air résiduel en espace de tête ou si le produit est emballé sous vide…
Nous avons également déterminé une taille de fuite minimale que nous voulons détecter pour garantir la durée de vie du produit, mais aussi qu’il soit transporté dans de bonnes conditions jusqu’au client final.
Exemple de détermination des paramètres
Prenons par exemple un emballage flexible contenant des produits solides avec une quantité d’air résiduel d’environ 10 % à 20 %, nous voulons déterminer si l’on peut détecter sur ce produit une fuite d’environ 100 microns correspondant à un débit de fuite de 10-2 mbar.L/s.
Nous allons procéder par expérimentation, tous les paramètres seront déterminés par des expériences menées dans les laboratoires des emballeurs (société qui emballe des produits).
En effet, les différents acteurs sont responsables à hauteur de leurs rôles respectifs.
Par exemple, le fournisseur de la ligne d’emballage n’est pas responsable si le film utilisé n’est pas compatible avec le produit final. De même que le fournisseur de film plastique n’est pas responsable si l’emballeur utilise mal la machine qui doit utiliser le film et le sceller…
C’est l’emballeur qui est responsable de vérifier qu’une fois le processus d’emballage réalisé, le produit est bien emballé et que l’étanchéité est conforme à ce qui est attendu.
- Première étape
La première étape est de rassembler des échantillons sur la ligne de production que ce soit en phase de production ou en phase de qualification de l’emballage.
Une fois que nous avons 10 échantillons, nous allons réaliser des trous calibrés dans ces échantillons. Idéalement, ces trous doivent être proches de la valeur que nous devons détecter.
Pour notre exemple, si l’on veut détecter 100 microns, il nous faut des échantillons sains (sans fuite), des échantillons avec des fuites de 50, 100 et 150 microns.
Une fois que les échantillons sont troués et identifiés correctement avec les valeurs des fuites respectives, nous allons commencer à utiliser une technique simple de test par le vide en immersion.
Je rappelle que notre produit est un emballage flexible contenant des produits solides et 10 % d’air résiduel en espace de tête.
Les premiers échantillons testés sont les échantillons qui présentent la plus grosse fuite.
- Deuxième étape
On place les échantillons en immersion dans notre chambre à vide et on applique graduellement plusieurs paliers de niveau de vide successif de -50 mbar en -50 mbar (-50, -100, -150…) jusqu’à détecter cette première fuite de 150 microns.
Imaginons pour notre exemple que la fuite, au travers de notre trou de 150 microns, est détectée à -250 mbar au bout de quelques secondes à ce palier.
Cela nous donne une première valeur de référence. Un deuxième échantillon avec fuite de 150 microns peut être utilisé pour confirmer ou ajuster cette première valeur de référence.
Pour les fuites plus petites pas la peine de répéter tous les paliers inférieurs à -250 mbar, on teste juste un ou 2 paliers à -100 mbar et -200 mbar par exemple. Ensuite on recommence nos tests incrémentaux avec les échantillons qui présentent une fuite de 100 microns.
Ainsi on continue nos tests de -50 mbar en -50 mbar à -250, -300…jusqu’à détecter la nouvelle fuite de 100 microns. Imaginons pour notre exemple que la valeur se trouve à -400 mbar.
On note cette valeur de référence pour les échantillons avec fuite de 100 microns.
On continue notre investigation avec les échantillons présentant une fuite de 50 microns. Cette fuite représente une limite visuelle de détection des bulles.
On recommence notre série de paliers avec des niveaux de vide successifs sur ces nouveaux échantillons.
Nous commençons donc directement à -400 mbar avec ces fuites, ensuite nous continuons de -50 mbar en -50 mbar jusqu’à détecter notre fuite de 50 microns. Il est possible que nous ne puissions pas voir la fuite, car la limite de détection est atteinte. Nous pouvons si c’est possible faire des essais avec des échantillons avec des fuites de 70 microns ou 80 microns.
On note ensuite toutes les valeurs dans un tableau.
Le niveau de vide nécessaire pour détecter la fuite et le temps qu’il faut pour que les premières bulles apparaissent. Souvent, lorsqu’on atteint un palier, la détection est immédiate, mais on peut tester avec des valeurs légèrement inférieures pour voir si l’on arrive à détecter quelques bulles au bout d’un temps plus important.
Voici donc notre tableau récapitulatif.
Diamètre de la fuite témoin | Niveau de vide de détection de la fuite | Temps nécessaire pour la détection |
150 microns | -250 mbar | 1 sec |
100 microns | -400 mbar | 1 sec |
50 microns | Non détectable | Non détectable |
80 microns | -600 mbar | 1 sec |
Nous remarquons ici que si l’on va au-delà de -600 mbar, on détecte toutes les fuites dont le diamètre est supérieur à 80 microns.
Cette valeur peut donc nous servir de référence pour nos fuites de 100 microns. En effet, si nous détectons des fuites plus petites, c’est encore mieux pour la qualité des produits testés. Sans atteindre des valeurs extrêmes, le compromis peut être intéressant.
Nous avons donc déterminé notre valeur de référence pour ce produit en particulier.
Ce protocole doit être mis en place pour tous les types de produits même si on utilise des emballages similaires avec les mêmes matériaux pour emballer des produits différents, le volume d’air résiduel ainsi que le comportement de l’emballage peut être complètement différent d’un produit à l’autre. Tous les paramètres doivent être adaptés en fonction du produit qui est testé.
En ce qui concerne le temps de test à un niveau de vide déterminé.
Si nous testons le produit pendant 1 minute à -600 mbar et que nous ne voyons aucune bulle apparaître, nous sommes certains que ce produit ne comporte pas de fuite de plus de 80 microns.
Pas la peine d’augmenter le temps à outrance, si les bulles doivent apparaître, elles apparaîtront rapidement. Il est même impératif d’être attentif, car les bulles peuvent sortir pendant un temps très court. En effet, lorsqu’une bulle se forme, de l’air s’échappe de notre emballage et la pression dans celui-ci tente de se stabiliser par rapport à la dépression que nous avons effectuée dans notre chambre à vide. Il est donc possible en fonction de la taille de l’emballage et surtout de la quantité d’air résiduel dans celui-ci que l’échappement des bulles ne dure que quelques secondes. Dans ce laps de temps, nous devons détecter visuellement un chapelet de bulle ou une bulle qui voit son volume augmenter. En effet, il faut être vigilant également, car certaines bulles peuvent être bloquées par des éléments structurels de notre emballage, des pliures ou des rabats peuvent bloquer l’échappement des bulles.
Il est impératif d’être très attentif lorsque l’on atteint un nouveau palier de niveau de vide lors d’un test nouveau sur un emballage témoin.
Ces techniques d’essai pour les emballages flexibles doivent être adaptées pour les tests des emballages de produits liquides dans des contenants rigides.
Nous verrons ces types de produits dans un prochain article.