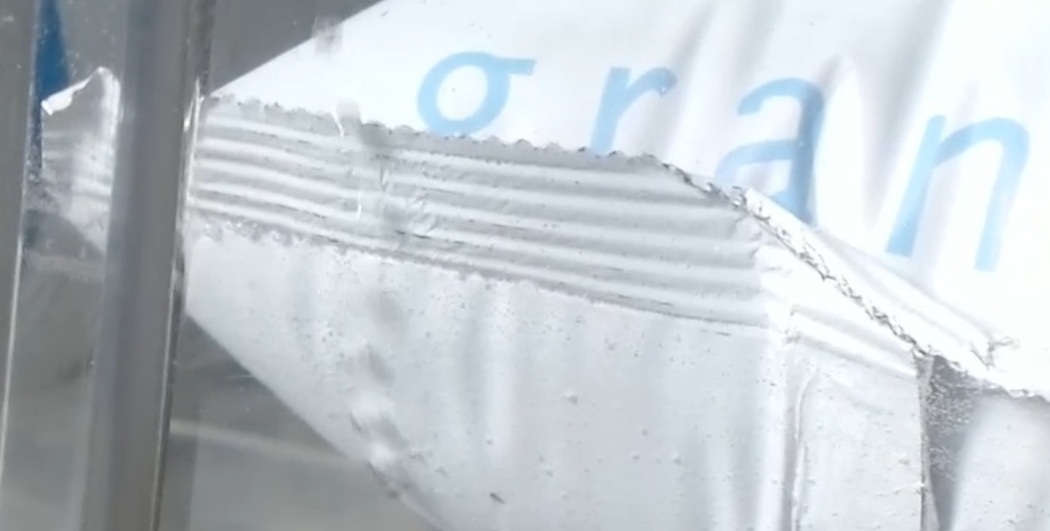
First, we need to know what we are looking for. Most of the time, we are trying to determine waterproofing, but waterproofing can be defined in many ways: waterproofing, vapour proofing, airtightness, bacteria proofing?
To determine this leak tightness, this ‘criterion’, we need to consider the product being protected.
Is this product sensitive to bacteria? In this case, we will look for leak tightness with a leakage rate of around 10-4 mbar.L/s
Is this product sensitive to vapour? In this case, we will look for a leakage rate of around 10-3 mbar.L/s
The more we want to go in terms of sealing, the more expensive the detection method will be…
Here is a small table that will give you some guidelines.
Criteria | Leak rate mbar.L/s | Leak diameter |
Watertightness | <1,0·10-2 | Ø ≈ 100 μm |
Vapour barrier | <1,0·10-3 | Ø ≈ 10 μm |
Bacteria-proof (shells, sticks, etc.) | <1,0·10-4 | Ø ≈ 1 μm |
Oil tightness | <1,0·10-5 | |
Virus barrier | <1,0·10-6 <1,0·10-8 <1,0·10-10 | Ø ≈ 0.3 μm Ø ≈ 0,03 μm Ø ≈ 1,0 nm |
Gas tightness | <1,0·10-8 | Ø ≈ 0.05 μm |
Absolute tightness | <1,0·10-12 |
Source : Jean-Marie CLAY – Leybold Vacuum
Once this ‘leakage criterion’ has been determined, we know the approximate size of the hole we want to determine. But it may not be a hole; it could also be a channel, which we will call a capillary, that will allow a certain leakage flow rate.
It is essential to correlate the size of the leak with the associated leak flow rate. For certain methods, we will compare the actual flow rate observed on our sample with the theoretical flow rate from which we want to determine the leak.
Once these two parameters are known, i.e. the size of the leak and the leak rate, the teams responsible for packaging and the teams responsible for the product must be consulted. All stakeholders must sit down together, as it will be difficult to determine the leak-proofness if the material used for packaging is not known. For example, all porous packaging is difficult to evaluate in terms of leak tightness, as the porosity varies depending on the material.
It is also important to involve the R&D teams to avoid designing packaging that is too complex to test. For example, very thin products are difficult to pierce with a needle, and opaque materials can block visual detection of leaks or dye penetration.
All the variables in our equation are important.
We now have a thorough understanding of our material, our product, how it is packaged, whether there is residual air in the headspace, or whether the product is vacuum-packed.
We have also determined the minimum leak size we want to detect to guarantee the product’s shelf life and ensure that it is transported in good condition to the end customer.
Example of parameter determination
Let’s take, for example, flexible packaging containing solid products with a residual air content of approximately 10% to 20%. We want to determine whether a leak of approximately 100 microns, corresponding to a leak rate of 10-2 mbar.L/s, can be detected on this product.
We will proceed by experimentation, with all parameters determined by experiments conducted in the laboratories of the packagers (the company that packages the products).
In fact, the various parties involved are responsible to the extent of their respective roles.
For example, the packaging line supplier is not responsible if the film used is not compatible with the final product. Similarly, the plastic film supplier is not responsible if the packager misuses the machine that is supposed to use the film and seal it.
It is the packager who is responsible for checking that, once the packaging process is complete, the product is properly packaged and that the seal is as expected.
- First Step
The first step is to collect samples from the production line, either during production or during the packaging qualification phase.
Once we have 10 samples, we will drill calibrated holes in them. Ideally, these holes should be close to the value we need to detect.
For our example, if we want to detect 100 microns, we need healthy samples (without leaks) and samples with leaks of 50, 100 and 150 microns.
Once the samples have been punctured and correctly identified with their respective leak values, we will begin using a simple immersion vacuum testing technique.
Remember that our product is flexible packaging containing solid products and 10% residual air in the headspace.
The first samples tested are those with the largest leaks.
- Second Step
The samples are immersed in our vacuum chamber and several successive vacuum levels are gradually applied in increments of -50 mbar (-50, -100, -150, etc.) until the first leak of 150 microns is detected.
Let’s imagine for our example that the leak, through our 150-micron hole, is detected at -250 mbar after a few seconds at this level.
This gives us an initial reference value. A second sample with a 150-micron leak can be used to confirm or adjust this initial reference value.
For smaller leaks, there is no need to repeat all the levels below -250 mbar; we just test one or two levels at -100 mbar and -200 mbar, for example. Then we repeat our incremental tests with the samples that have a 100-micron leak.
We continue our tests from -50 mbar to -50 mbar to -250, -300, etc., until we detect the new 100-micron leak. Let’s imagine for our example that the value is -400 mbar.
We note this reference value for samples with a 100-micron leak.
We continue our investigation with the samples with a 50-micron leak. This leak represents a visual limit for bubble detection.
We are resuming our series of stages with successive vacuum levels on these new samples.
We are therefore starting directly at -400 mbar with these leaks, then continuing from -50 mbar to -50 mbar until we detect our 50-micron leak. It is possible that we will not be able to see the leak, as the detection limit has been reached. If possible, we can test samples with leaks of 70 microns or 80 microns.
We then record all the values in a table.
The vacuum level required to detect the leak and the time it takes for the first bubbles to appear. Often, when a plateau is reached, detection is immediate, but we can test with slightly lower values to see if we can detect a few bubbles after a longer period of time.
Here is our summary table.
Diameter of the test leak | Leak detection vacuum level | Time required for detection |
150 microns | -250 mbar | 1 sec |
100 microns | -400 mbar | 1 sec |
50 microns | Not detectable | Not detectable |
80 microns | -600 mbar | 1 sec |
We note here that if we go beyond -600 mbar, we detect all leaks with a diameter greater than 80 microns.
This value can therefore serve as a reference for our 100-micron leaks. Indeed, if we detect smaller leaks, this is even better for the quality of the products tested. Without reaching extreme values, the compromise can be worthwhile.
We have therefore determined our reference value for this particular product.
This protocol must be implemented for all types of products, even if similar packaging with the same materials is used to package different products, as the residual air volume and the behaviour of the packaging can be completely different from one product to another. All parameters must be adapted to the product being tested.
With regard to the test time at a given vacuum level.
If we test the product for 1 minute at -600 mbar and see no bubbles appear, we can be sure that this product has no leaks larger than 80 microns.
There is no need to increase the time excessively; if bubbles are going to appear, they will appear quickly. It is even imperative to be attentive, as bubbles can escape in a very short time. When a bubble forms, air escapes from our packaging and the pressure inside it attempts to stabilise in relation to the vacuum we have created in our vacuum chamber. Depending on the size of the packaging and, above all, the amount of residual air inside it, the escape of bubbles may only last a few seconds. During this time, we must visually detect a string of bubbles or a bubble that is increasing in volume. We must also be vigilant, as some bubbles may be blocked by structural elements of our packaging, such as folds or flaps, which can prevent the bubbles from escaping.
It is essential to be very careful when reaching a new vacuum level during a new test on a sample package.
These testing techniques for flexible packaging must be adapted for testing liquid product packaging in rigid containers.
We will look at these types of products in a future article.